How Aluminum Profiles Are Produced or Extruded
- Acumaster
- Apr 28, 2020
- 2 min read
Let me introduce you to our aluminum extrusion process, a process where in quality ISO grade billet is melted and transformed into the superior aluminum profiles ready for fabrication and assembly.
1. Machine start-up and mould preparation
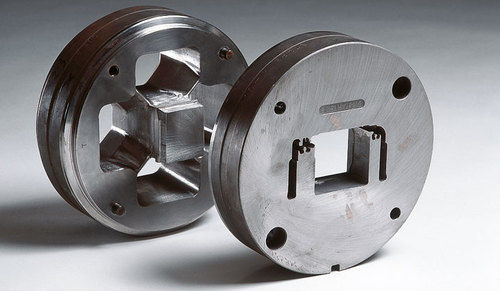
The first step in the aluminum production process is to prepare the machine for start-up together with the die mould to be used. The die mould is pre-heated in from 400-500 degrees celsius to ensure even flow of the aluminum and to maximize the die mould shelf life.
2. Aluminum billet pre-heat and transfer to extrusion press
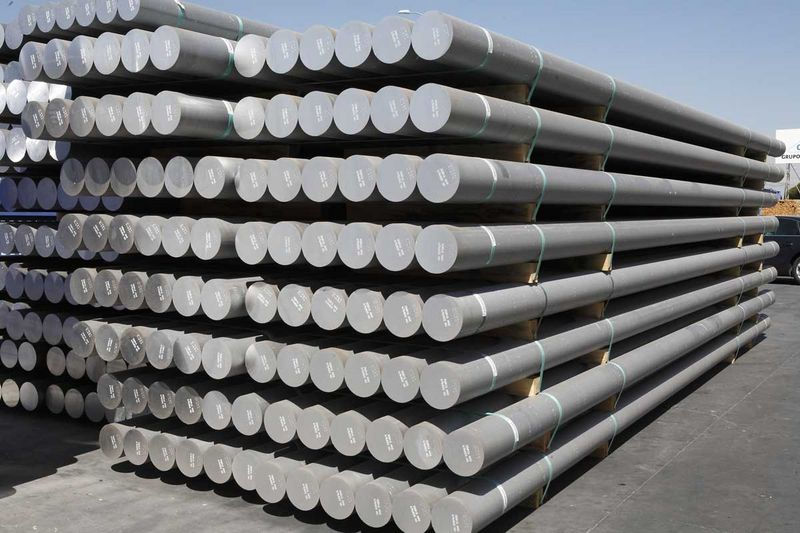
Second, our ISO grade quality aluminum billet, a solid cylindrical block of aluminum is cut from the longer log and is also pre-heated in an oven. With high temperature, the aluminum billet becomes malleable enough to be formed according to the die mould.
3. Extrusion rod pushes the billet into the container through the mould
Once the billet is at the right temperature and is ready for extrusion, the machine mechanically transfers this to the extrusion press. A lubricant is applied to the extrusion rod, the rod that will push the billet, to prevent the billet and the rod from sticking together.
4. Extruded aluminum comes out from the die mould

The extrusion rod will apply tons of pressure to push the malleable billet into the extrusion container until the container is filled with aluminum. Once the container is filled, the aluminum billet will flow through the die mould and will take its shape.
5. Item it guided by the puller on the runout bed and is cooled
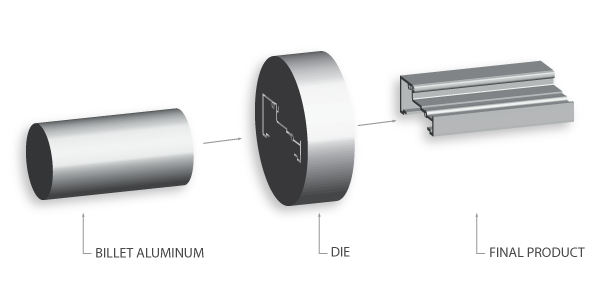
Next, the aluminum shaped by the mould goes above the runout bed for cooldown while being gripped by a puller that guides the aluminum being extruded from the press.
6. Aluminum profile is moved to the stretcher bed for correction
As the aluminum is pulled out of the press, some natural twists will occur which requires the item to be stretched in order to be corrected. The aluminum profile will be gripped by the machine on both ends and will stretch the profile until it is straight.
7. Aluminum is cut to desired length
The aluminum profile is then cut into the standard lengths of 12 and 21 feet accordingly except for the special orders which may go up to 24 feet or shorter.
8. Transfer aluminum into Aging Oven to reach standard hardness
But the process is not over yet. The aluminum has not reached the right temper at this point. In order to achieve the standard hardness, the profile is transferred by batch into the aging oven for up 4-8 hours.
9. Hardness test and other quality check measurements is done to ensure correct output
After the aging oven and other treatments such as the T6 process is done, hardness test is conducted again to confirm that hardness is according to the standard.
At the end of this whole process, we now have what we call a Mill Finished Aluminum profile. This profile is ready for use and assembly. But if colored or surface treated windows and doors is desired, a surface treatment is also needed. Read more about it here.
Comentarios